I usually don't endorse or review companies (I could start doing this if people want me to), but this is a company that stood out. I have been keeping my eye on
Freight Farms over the past year. It is basically an embodiment and harmony of both Greens and Machines. This new startup retrofits old shipping containers, turning them into self contained hydroponic growing units for greens, vining plants, and mushrooms. They currently only offer the "Leafy Green Machine" model which claims to produce 400 heads of lettuce per week. Recently, they ran a
Kickstarter to raise some cash to build a unit and get their footing and product to the market. Additionally, they have recently
sold a unit to a hotel in Concord, NH and
have sold a unit to a customer in San Antonio, TX. Personally, I think their idea and product concept is pretty good. Let's do some analysis.
Supply Chain
The company is incorporated in Boston, MA. Boston is one of the urbanized centers of the Eastern seaboard, meaning it is bound to have some abandoned lots. The company believes that it can find enough buyers in the city where container farms can supply entire city with fresh produce. Normally, cities like Boston would be importing tons of produce each month to meet the demand from consumers. All the importing requires fuel; it costs not only to the shipping companies, but the environment from the pollution produced by the vehicles used to bring goods to market. Vegetables, like beer and other goods, are the best tasting closest to the source and harvest date. Freight Farms emphasizes supplying the population with locally grown produce to ensure the customer receives the freshest possible product.
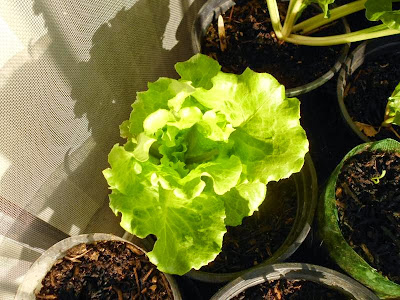 |
Nothing fresher than produce in your own backyard |
Like the phone in your pocket
Recently Boston passed a law allowing for urban agriculture in the city. This allows farmtrepreneurs (I made up a buzzword here, bear with me) to start growing within city limits. So what will some farmers want to do? Grow directly in the soil. Not all the lots in town are ideal for growing in the first place. From Boston's long past of industry, the ground and soil is likely tainted with heavy metals or other toxins that can be hazardous for both humans and plants. Growing hydroponically prevents any soil contamination from past pollutants. Additionally, Boston is very cold and has below freezing temperatures for at least 4 months out of the year. The option for many would be to invest in a greenhouse or high tunnel technology for year round growing. Freight Farms combines these two aspects into one unit by stuffing the hydroponic system in a self contained unit. By using an insulated shipping container, users would be able to grow year round, as they wouldn't need to worry about freezing temperatures or soil contamination. It would make sense for a company based in Boston to implement container growing (literally a shipping container) in their city.
Stacking Legos
The model of containing the unit inside a shipping container is attractive to the company because it allows for their farms to be modular and mobile. Those containers are built for stacking, and the farm units can be stacked high and wide on each other. This allows for vertical space to be utilized in addition to horizontal space. That's perfect if you want to fit a stack of containers in an
alleyway abandoned lot between two high-rises. The only real critique here is that the use natural lighting is out of the picture, as implementing a glass room would be essentially pointless if the container is covered by another one. The glass would not only be an expensive addition to the container, it would probably weaken the structural integrity and make it more prone to vandalism. Who knows; a kid could throw a rock off a building next to a container and compromise the roof (break the glass), destroying a whole cycle worth of lettuce due to freezing temperatures (I heard the MBTA had problems with kids throwing rocks at locomotives in the past). Additionally, since the container is mobile, you can put it move it almost anywhere. If the landlord decides that rent is going up, just bring in a truck and haul your container away, easy peasy. Thanks to their mobility, fresh produce can come from any little street corner in any city.
 |
Lettuce, but more density packed... and with greater growth control |
Intermodal containers are both cheap and abundant. I have heard they have warehouses sitting in the Midwest stacked full of containers because it would cost more to ship the empty ones back from where they came (China) than it would to build new ones there. Since our country's trade deficit with China is far in the negative direction, we are left with a bunch of shipping containers lying around. A
quick search of eBay shows me that I can get a 40' x 8' container from anywhere between $2000 and $5000, depending on location and quality. Getting the container isn't the only step though; it needs to have a bunch of stuff installed to make it suitable for growing. It needs insulation, a climate control system, plant growing systems, lighting, plumbing, an electrical source to power all the systems, and the skills to complete installation. This is where the bulk of the cost comes in.
Will the greens bring the green?
According to the claim from their website and video, each container can produce 400 heads of lettuce per week. Let's do some math. In a 40' x 8' container, if the walls and middle section are lined and maxed to capacity with plant growing spaces, I calculate 80 plants per row by 9 stacked vertical by 10 rows horizontal. My assumptions included leaving enough movement space on either side of the container (1.5 feet each side), a spacing of around 6 inches for all plants horizontal and 10 inches vertical. This gives a total of 7200 plant slots. I didn't take into account any climate control or ease of access for the user/operator though, which will knock that number down considerably. Personally, I think that number is very unrealistic, but it is a theoretical maximum. Instead, I will calculate the number of slots required to get 400 heads of lettuce per week. If we assume that the variety of lettuce is harvested every month (4 weeks) in a succession planting cycle, then the required slots is 1600. For 5 weeks this number is 2000, for 6 weeks 2400, etc (slots needed = number of plants per week*number of weeks). Most lettuce seed packets say that the plant grows in about 50 days, or 7 weeks. In a souped-up hydroponic system like Freight Farms, that number is probably closer to the 4-6 week time frame (the Kickstarter claims a full harvest cycle is 5 weeks). Based on this result, it would be better for the plants to get more spacing, at around 8 inches each side by 12 inches vertically. This calculation still accomplishes the target plant sites, allowing for around 3000 plants. If the full harvest cycle is 5 weeks, then there is a lot of space freed up by only needing 2000 sites to install all of the necessary components for growing lettuce. This is only for the 40' x 8' container though, Freight Farms did advertise using a 53' x 8.6' model on their Kickstarter. I don't know how easy it is to acquire that kind, but sticking to one size model is better for maintenance and stackablity.
 |
Your lettuce will look as good as mine! |
So you are producing 400 heads of lettuce a week. Nice. How much does lettuce cost per head in your market area? Where I am, it's about $2-$2.50 per head at the grocery store. Depending on who you'd sell to, you might get the same price based upon your limited supply from one container. And since it's high quality and in the middle of winter, let's say you can get $3 a head. That's $1,200 a week in revenue, not bad! How soon will you make your ROI though? Let's assume that the only cost you have is buying the unit itself; we'll ignore running costs, utilities, rent, etc for now. If it costs them $26,040 in materials to build one unit, then the finished product will end up costing $30,000 - $35,000 depending upon how far away from Boston you are. This cost is an estimate. Regardless, at $1,200 a week, the ROI period is about 27 weeks. That isn't too bad actually. With all the running costs, I'm assuming the $1,200 revenue will turn into somewhere around only $400-$600 in profit, upping that payback period to 55-110 weeks. That isn't too bad of a deal at all, considering that many companies usually have 5-7 year ROIs for large pieces of equipment. This is a super simplified model though, and is subject to change on many factors.
Aside from just crop revenue, you as a company or individual get the benefit of free PR and advertising. You are one of the few producers of fresh produce in town during the winter. Your produce is also very high quality compared to your competitors. You are the embodiment of the green movement from saving on transportation costs. Owning one of these Leafy Green Machines will help your image a lot. It'll be hard to not sell all your crop with all the press surrounding you. You need to act quick though, the competitors are finding out about Freight Farms while you just sit there...
Final Thoughts
If you are looking into joining the agriculturally revolution and want everything in one little package, consider Freight Farms. They will give you a farm in a box. For its cheap cost and high output, it would be foolish to not consider starting a produce farm chain in your local metropolitan area. I would personally buy one too if I had some extra dosh lying around, but alas, I am just a poor student at the moment. I hope to see this company take off and revolutionize the way we do food in urban areas.
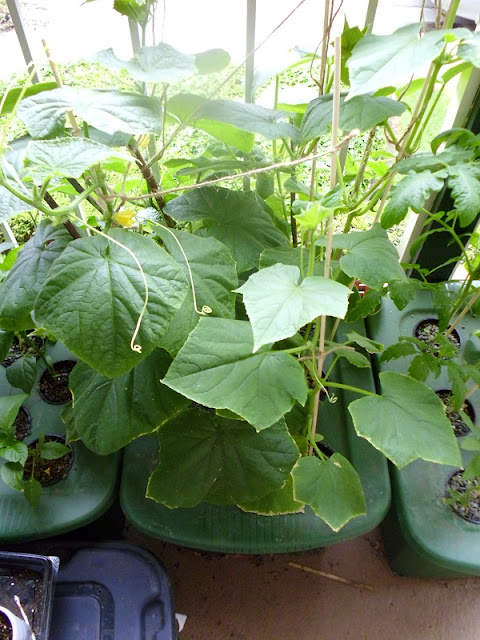 |
If my cucumber plants grew this big, I can't imagine how the company will do the spacing for the vine crop unit |
That's pretty crazy. As you point out, their numbers seem a bit high, but I do think it's cool what people come up with using these containers.
ReplyDeleteTo finish this cost analysis on ROI, one must consider operations cost. In controlled environment food growth especially, the energy consumption is the largest barrier and hinders profit substantially. I guarantee the ROI is no where even close to 5 years, and likely closer to 7-8 years, IF the heads of lettuce are large and healthy.
ReplyDeletehttps://www.freightfarms.com/case-studies/
ReplyDelete